
SH-TB823 sticking labels on small vials
For setting up your labeling machine, you will need the whole set of tools like different sizes of hex wrenches, normally the tool kit will be sent together with the machine. It will takes you about 30-40 minutes to read and understand this article, and takes you about 2-3 hours to setup the labeling machine.
Before the setup tutorial, we will briefly introduce the basic information of the labeling machine. The following is the outline of this article, which can be quickly browsed according to what you need to know.
- What is a labeling machine and what is the labeling machine used for
- Advantages of using labeling machine
- Types of labeling machines
- How to set up the labeling machine
- Common problems in the process of setting up the labeling machine
1. What is a labeling machine called and used for ?
A labeling machine is a piece of equipment used in manufacturing and packaging to put pre-printed labels onto various types of products, bottles, boxes and packaging bags etc
2. What are the advantages of labeling machine?
①Improves working capacity : take an example, SH-TB200R can reach 150 bottles/min
②Reduce production error rate: Normally label error is about 1mm, some machine can be 0.5mm
③Improve labor availability or reduce labor costs
3. Types of labeling machine
4. How to setup your labeling machine
Step1: Install the label roll
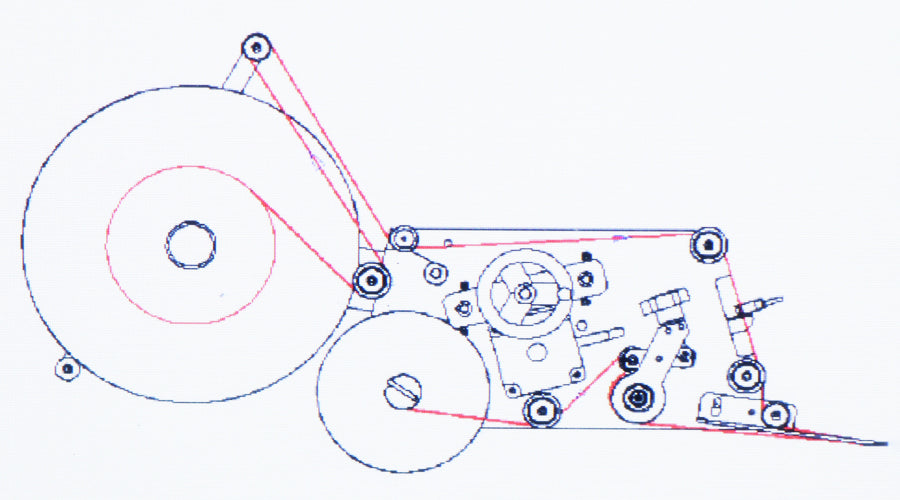

Step2: Understand the operating system of the machine
Usually, the name of the function button is displayed as briefly as possible on the operation panel of the machine to help understand the function of the corresponding button. We recommend that you ask the manufacturer of the machine for an introduction to the machine's control system, which is simpler and less risky to operate. If there is no corresponding introduction, you can choose to click each button in the operation panel in the manual mode of the machine (the button displayed as "manual" in the operation panel) to observe which components in the machine are running and the operating conditions, so as to Can understand the function of the button more clearly. Normally what we need to adjust will include "label outputting speed", "delay time to output labels", "delay time to stop outputting labels", for three roller labeling machine, 3 extra working data need to be adjusted, they are "bottle clamping time", "delay time to clamp bottles" and "interval time for front and back labels"

Step3: Adjust the width of the conveyor belt according to the labeling objects
Loosen the fixed knobs on both sides of the conveyor belt guardrail, adjust the width of the conveyor belt guardrail according to the diameter or width of the labeling object to ensure that the object can just pass through, and then tighten the fixed knobs on both sides to complete the conveyor belt width adjustment work.

Step4: Adjust the position of the labeling structure according to the labeling object
Step 4-1: The first thing to adjust is the amount that the label overhangs the dispensing edge, we also called it label outputting length. If label outputting length is not adjusted to the appropriate data, it is likely that the label will be repeatedly pasted on the labeling object or the label cannot be attached to the product. Adjusting the label outputting length to 3-5mm can solve these problems well. There are two ways to adjust the label outputting length. ①Adjust the "delay time to stop outputting labels" ②Adjust the position of the label sensor.
But how to do that?
①Adjust the "delay time to stop outputting labels": Normally we need to set the delay time to the minimum value, such as 0.01s or 0.1s, and then click the "Manual" button to check the label outputting length, and confirm whether to increase the parameter value according to the actual effect until the label outputting length is 3-5mm
②Adjust the position of the label sensor: When the label sensor detects the label, it will send a signal to the control system to make the machine dispense label stickers. When the label sensor detects the back paper (usually the gap between the label and the label), no work order will be sent and the label will not be dispensed. Based on the rolling direction of the label roll (the side that is dispensed first is the front side, and the other side is the rear side), the closer the label sensor is to the front, the longer the label outputting length will be. The closer the label sensor is to the rear, the shorter theoutputting length will be.
Step 4-2:Adjust the position of labeling object sensor
The labeling object sensor will send a signal to the control system when it detects passing by labeling object, so that the machine can attach the label to the products. When the labeling object sensor cannot detect the labeling object, no work order will be sent, and the machine will not attach the label to labeling objects. Due to the labeling structure will be different according to the labeling object, the position of labeling object sensor is not fixed. But I have some advice for reference
①For three roller labeling machine: the labeling object sensor is usually necessary to install the labeling object sensor directly above the labeling object to ensure that it can sense the labeling object.
②For labeling machine with press belt: The labeling object sensor is usually placed at a distance of 5mm from the labeling belt
③Double side labeling machine: The labeling object sensor usually needs to be as close as possible to the label separating plate
④Top side labeling machine: The labeling object sensor is usually placed at a distance of 5mm from the label separating plate.
Are you also curious about what will the position of the labeling object sensor influence on the labeling effect?
In generally, based on the running direction of the conveyor belt (the side close to the labeling structure is the right side , and the other side is the left side), if the position of the labeling object sensor is closer to the right, the labeling object will be detected later. The sticker will also be labeled more to the left.
Top side labeling machine/Double sides labeling machine These two types of machines will need to pay attention to the adjustment of this position. Different from other labeling structure, for the three-roller labeling structure, it is also need to ensure the labeling objects sensor should match with the position of the running speed of the conveyor .When the labeling object sensor detects bottles, it will control the clamping structure to fix bottles and finish the labeling work, so if your conveying speed is too fast, the clamping structure will not able to clamp bottles in time and vice versa.For labeling machine with pressing belt, If the labeling object sensor position is too close to the labeling structure, then there are some bubbles under self adhesive stickers or the label will be arched.If the position is too far from the labeling structure, the labels may can not be sticked to the labeling object or the label roll may be rolled or pulled during the labeling process
Have you ever thought about this question, how can we ensure that the sensor detects the label or labeling object?
Actually, due to the different types of sensors, the way of displaying information will also be different. When some sensors detect objects, the lights will be on, and when the objects are removed, the lights will be off. There are also some sensors, when an object is detected, a "|" symbol will appear on the sensitivity adjuster equipped.
Step 4-3:Adjust the position of labeling structure according to labeling object
① Three-roller labeling machine
The labeling assembly of this type of labeling machine consists of three rollers combined. Put the object to be labeled (usually a standard cylinder) between the three rollers, so that the distance between the object and the separated label part is 3-5mm. While making sure the air compressor is not connected, loose screws used to fix the position of the labeling component consisting of two rollers and push this labeling component to another side. It is necessary to ensure that the labeling object can be just clamped by the three rollers. If the labeling object is clamped too close, the labeling object will be suspended above the conveyor belt during labeling and cannot be labeled well. If the labeling object cannot be clamped, there will be some bubbles under label stickers or labels can not be attached to the labeling object, the labeling effect is not ideal. After adjusting the position of the labeling component consisting of two rollers, it is necessary to re-tighten the screw to fix position.


In addition, if you need to use a three-roller labeling machine to realize front and back side labeling, you need to adjust the distance between the front and back labels. Usually, the interval between the front and back labels can be set through the operating system. We need to set the interval time to the minimum value, such as 0.01s or 0.1s, and then click the "Manual" button to detect the labeling effect, and confirm whether to increase the parameter value according to the actual labeling effect until you get the good labeling effect.In addition, the The rotation speed of the three rollers should match the label outputting speed.
A. If the label outputting speed is faster than rotating speed, then then there are some bubbles under self adhesive stickers or the label will be arched.B. If the label outputting speed is slower than rotating speed, the label roll may be rolled or pulled during the labeling process.
②Labeling machine with press belt
After adjusting the label outputting length, this type of labeling machine needs to adjust the distance between the pressing belt and the pressing belt according to the diameter or width of the labeling object to ensure that the bottle can just pass through and the labeling object will not be stuck. After that, confirm whether the running speed of the pressing belt match with the label outputting speed.
A. If the label outputting speed is faster than running speed of press belt, then then there are some bubbles under self adhesive stickers or the label will be arched.B. If the label outputting speed is slower than running speed of press belt, the label roll may be rolled or pulled during the labeling process.
③Double sides labeling machine
The adjustment method of this type of labeling machine is similar to that in ②. After adjusting the distance between the label separating plates on both sides according to the width and diameter of the labeling object, it is necessary to confirm whether the conveying speed is consistent with the label outputting speed.

a-1: The part of sticker will be labeled, another part won't
a-2: There are some bubbles under self adhesive stickers or the label will be arched.
a-3: The sticker can not be labeled to the product
a-4: The sticker will be labeled to the front side of products
B. If the label outputting speed is faster than conveying speed, it may caused the sticker will be labeled to the rear side of products
④Top side labeling machine
There are many factors that affect the labeling position of this type of labeling machine. In addition to the front and rear / left and right / up and down positions of the labeling components, the position of the label sensor / the position of the labeling object sensor / the consistency of the conveying speed and the label outputting speed will affect the labeling effect. First of all, it is necessary to adjust the front, back and left and right positions of the labeling structure according to the production need. The operator can adjust the position of the labeling structure through rotary knobs of the labeling structure. The label separating plate should be 3-5mm higher than the upper plane of the labeling object. If the label separating plate is too high, the label cannot be attached to the product. If the label peel plate is too low, the labeling object will be jammed or there will be some bubbles under stickers.
Same as the double sides labeling machine, we need to make the label outputting speed match with the conveying speed.
A. If the label outputting speed is faster than conveying speed, it may caused : the sticker will be labeled to the front side of productsB. If the label outputting speed is faster than conveying speed, it may caused :the label will be labeled to the rear side of products
For the ①②③ labeling components, the following two labeling effects may also appear during the labeling process
A. the beginning of label is higher than the end of label, you need to use the rotary knob to lower the label separating plateB. the beginning of label is lower than the end of label, you need to use the rotary knob to heighten the label separating plate

Step 5. Adjust the speed of the conveyor belt
After adjusting the labeling structure, we need to adjust the conveying speed according to production need. There are usually buttons on the operation panel or the side of the machine body to individually control the running speed or the working status of the conveyor belt. Generally speaking, whether it is to speed up or slow down the running speed of the conveyor belt, we need to increase or slow down the labeling outputting speed (in order to ensure that the speed of the two can match). Therefore, once the speed of the conveyor belt is reaching the required speed, we need to readjust the label outputting speed based on labeling effect. You can refer to the step 4.
In addition, for three roller labeling machine, the bottle clamping time should match with the conveying speed. If not, it may caused:
A. The bottle clamping time is too long, several pieces of stickers will be sticked to same product.B. The bottle clamping time is too short, the label roll may be rolled or pulled during the process. or the part of label will be sticked, another part won't.
Step6. Adjust the "delay time of outputting label"
Generally speaking, whether it is to speed up or slow down the running speed of the conveyor belt, we need to increase or slow down the labeling outputting speed (in order to ensure that the speed of the two can match). Therefore, once the speed of the conveyor belt is reaching the required speed, we need to readjust the label outputting speed based on labeling effect. In this situation, we need to adjust the "delay time of outputting label" to make the label outputting speed match the running speed of the conveyor belt.
A. If the "delay time of outputting label" is too short, it may caused:a-1: The front half of the label is folded, and the second half can be attached to the object normally.(For three roller labeling machine and labeling machine with press belt)
a-2: The sticker will be labeled to the front side of products (For double sides labeling machine and top side labeling machine)
B. If the "delay time of outputting label" is too long, it may caused:a-1: The part of sticker will be labeled, another part won't.(For three roller labeling machine)
a-2: The sticker can not be labeled to the product (For labeling machine with press belt)
a-3: The sticker will be labeled to the rear side of products (For double sides labeling machine and top side labeling machine)
Step 7. The function of delay to stop outputting label (Optional)
Usually in the control system of the labeling machine, you can see the "delay to stop label" function button. As mentioned above, it can be used not only to control the label outputting length. It also has another function. In the actual operation process, we found that when the label is too long, if only the above-mentioned machine parts are adjusted, the label still cannot be perfectly attached to the item. At this point, the operator can set the time value for the delayed stop. Usually we recommend to start with the minimum value, and then test the labeling effect several times until you get the good labeling effect.
Step8: Adjust the date coder(Optional)

B. If the indentation of the font on the label is too shallow, you need to tighten the screws in the figure below to adjust the stroke of the coder

D. If the indentation of the font on the label is appropriate, but the printing color of the font is too light, this is caused by the temperature of the coder being too low. At this time, it is necessary to increase the temperature of the coder
Common problems in the process of setting up the labeling machine
- If labels are pasting up and down from the end, one end is slightly up and other down , what is the solution to paste label evenly?

- How to control label shifting problems in flat bottle
- The sensor doesn't seem to recognize labels/backing paper as some of our labels are similar colors to the backing paper, what is the solution to this?
- How to determine label roll direction?

- The labeling machine can not dispense labels, what can i do?
- There are some bubbles under stickers, what is the solution to paste label evenly
-
The machine keeps dispensing labels, how to solve this?
Check if the label sensor can detect labels correctly. If yes, then something is wrong about the labeling object sensor. You need to adjust the sensitivity of labeling object sensor .If not, adjust the sensitivity of the label sensor and try to see if labels can be detected. - The machine dispense several pieces of labels, how to solve this?
- There is a crack on the edge of the bottom paper of the label, what is the solution to this?
Step 1. Install the label roll
Step 2. Understand the operating system of the machine
Step 3. Adjust the width of the conveyor belt according to the labeling objects
Step 4. Adjust the position of the labeling structure according to the labeling object
Step 5. Adjust the speed of the conveyor belt
Step6. Adjust the "delay time of outputting label"
Step 7. The function of delay to stop outputting label
Step 8. Adjust the date coder
Based on the above tutorial, you will know the direction to setup common self-adhesive sticker labeling machine. If you still need any help to setup labeling machine or don't know how to choose a labeling machine, please send e-mails to info@sunhanpack.com, we will reply you in 24 hours.